Why Use Boat Foam?
- Buoyancy
- Safety - prevention from capsize
- A more stable vessel
- A more consistently supported deck
- Sound deadening
Marine buoyancy or commonly asked for as “foam used in boats”, is available in several different materials namely, sheet foam as either expanded polyethylene (EPE) or the chemically cross-linked polyethylene (XPE) or liquid pour polyurethane (PU) expanding foam. Check out the basic explanation we have put together below to answer your question, “why use boat foam?”
The most obvious answer to “why use boat foam?” is buoyancy. In its simplest terms, this is the material’s ability to exert an upwards force known as buoyant force, but we will cover this in a future article for all those techies out there. Closed cell foam, such as XPE and EPE, is naturally buoyant, doesn’t absorb water and is easily worked into any shape or block you might require making them very common products for marine buoyancy.
Safety should be another important reason why these foams are used as boat foam. Marine buoyancy can prevent your vessel from capsizing and help keep you stable in rough seas or moving around the vessel.
Finally, foam is a great sound absorber and deflector to reduce any excess noise. Foam is so good as both a sound absorber and deflector, it is commonly used in acoustic and insulation applications outside of its use in boats.
Foam Sheets Compared to Liquid Pour Foams (PU Expanding Foams)
When deciding on which foam to use as a boat foam, there are a few different options you will read about. Two of these are sheet foam and the other is a liquid pour or PU expanding foam (PU). Our basic explanation below of what to consider will help when selecting which boat foam might be best for you.
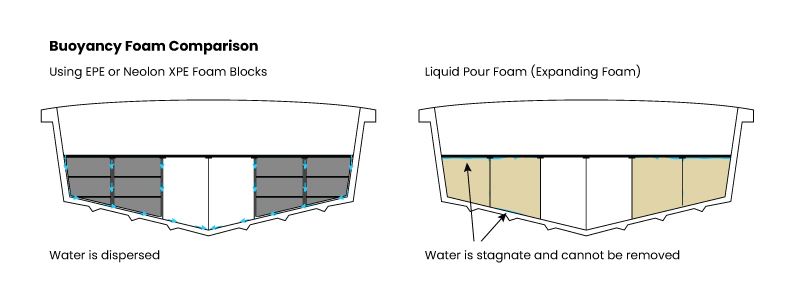
Sufficient Drainage
Liquid pour boat foam or PU expanding foam can fill the void a little too well and prevent water from being able to reach the transom or bilge pump. When refurbishing a boat, it is commonly reported that stagnant water is sitting in the hull by not being able to exit through the transom or bilge pump. This is not always water from those sunny days out running your boat, it can also be water ingress from rainwater while your boat is not in use if sufficient drainage is not considered.
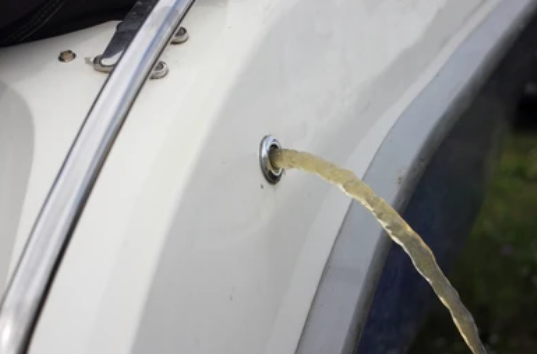
Unlike PU foams, water cannot be absorbed by closed-cell foams which comply with ASTM or JIS testing standards. The testing was done and found that after 48 hours submerged in water the foam only retained 0.00009/cm3, essentially water proof. High quality foams maintain their structural rigidity to keep any water egress pathways clear.
Longevity
Liquid pour boat foams are known to shrink, absorb water and deteriorate depending on what type of expanding foam is used. A quick search on the internets results in many different experiences and opinions.
Sheet foams can suffer from the same fate depending on which sheet foam you choose however there are two main choices which provide tangible benefits over a liquid pour PU foam, these include expanded polyethylene, commonly known as EPE, or chemically cross-linked polyethylene, commonly known as XPE.
EPE and XPE perform very differently as marine buoyancy, you can compare all the features and benefits of the 2 foams here: PJ Bowers Marine Buoyancy Foam. The basic longevity of EPE is five to seven years with XPE last over 20 years.
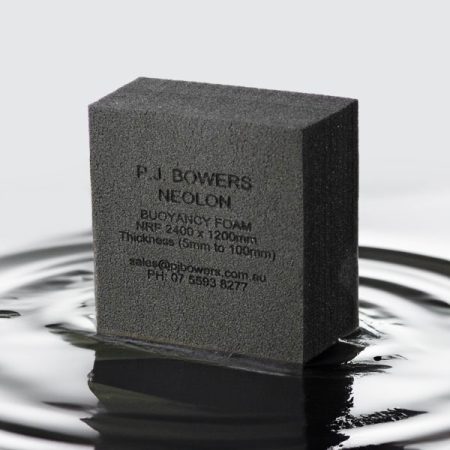
Ease of Replacement
If you have made it this far, your selection is either PU foam or sheet foam. One of these choices is much easier to replace than the other. PU foam is clearly the more difficult choice as it bonds to the substrate and, being a liquid, makes its way into every nook available meaning removal can be difficult and time consuming and often wet and smelly. Removal of PU foams requires cutting large slabs into smaller blocks then leveraging these blocks out with a tool, then scrapping or grinding off any excess. If this sounds like hard work, it is.
As seen in my videos online such as the example below, which can be watched here: https://www.youtube.com/watch?v=fMBdKNVUYvg
For ease of replacement, sheet foam is much simpler. Simply remove the foam slabs and any other foam shapes from the void and refill. Unlike PU foams, removing sheet foam is not chemically bonded or hardened and no special tools are required.
Once you remove any old boat foam and move to the next step of installing your new foam, the benefits of sheet foam continue. PU foams require mixing, time wasted while the chemical reaction takes place and can be hazardous if used incorrectly. With sheets foams, simply cut to size and put in place. Should you make a mistake, you can simply recut and replace rather than having to start again.
Type of Sheet Foam as Marine Buoyancy
The first recommended sheet foam is expanded polyethylene or commonly known as EPE. This is a very frequently used boat foam and is approved by NATA for marine use. The benefits of EPE are it has low water absorption, is cheap, readily available and won’t block water paths resulting in moisture sitting in the hull. EPE foam is mainly used the packaging industry in place of polystyrene and therefore there are some detractors of using EPE which include a short lifespan of only five to seven years and it is not approved to be used in commercial vessels. You can access the EPE technical data sheet (TDS) here.
Neolon cross-linked polyethylene, or known as Neolon XPE, is the second sheet foam and the foam sheet of choice. Neolon XPE benefits far outweigh any cost difference which include;
1. 20-year lifespan which could save you four times the amount of work, especially if your boat foam is positioned in a fully welded section.
2. Approved for use in commercial vessels which demonstrates its high quality.
3. Fuel resistant reducing the risk of the material breaking down.
4. Flame retardant reducing the risk of fire onboard your boat due to ignition issues or sparks.
5. Water Resistant which ensures longevity of the material and reduced need for replacement.
6. High structural integrity of the material providing confidence that moisture will be able to exit where it is meant to through the transom or bilge.
7. Readily available and easily workable allowing you to complete any works required should you feel up to the task.
You can access the Neolon XPE technical data sheet (TDS) here.
Please note: It is extremely important not to use black EPE in any outdoor or marine application. Black EPE is not suitable for any marine buoyancy or general marine use.
For ease of replacement, sheet foam is much simpler. Simply remove the foam slabs and any other foam shapes from the void and refill. Unlike PU foams, removing sheet foam is not chemically bonded or hardened and no special tools are required.
Once you remove any old boat foam and move to the next step of installing your new foam, the benefits of sheet foam continue. PU foams require mixing, time wasted while the chemical reaction takes place and can be hazardous if used incorrectly. With sheets foams, simply cut to size and put in place. Should you make a mistake, you can simply recut and replace rather than having to start again.
Where to From Here?
If you have considered all the points in this article, you’ll likely be able to choose what boat foam is right for you. The choices are dependant on the function of your boat, it’s size and complexity of its design, how long you expect the material to last and how much effort you’re willing to exude.
If you would like an idea of how much boat foam you require, check out our Floatation Calculator here. You can easily understand how much sheet foam you require, then purchase your material through www.foamproducts.com.au for delivery to your door following secure payment.
If you are interested in more information on boat foam such as more detailed information on EPE or Neolon XPE or information on marine buoyancy and electrolysis in aluminium hulls, please see our articles here.